Hager Implements Sustainable Manufacturing
In a bid to reduce their environmental impact through the implementation of more sustainable initiatives, Hager have identified a number of measures that will significantly reduce the company’s energy consumption.
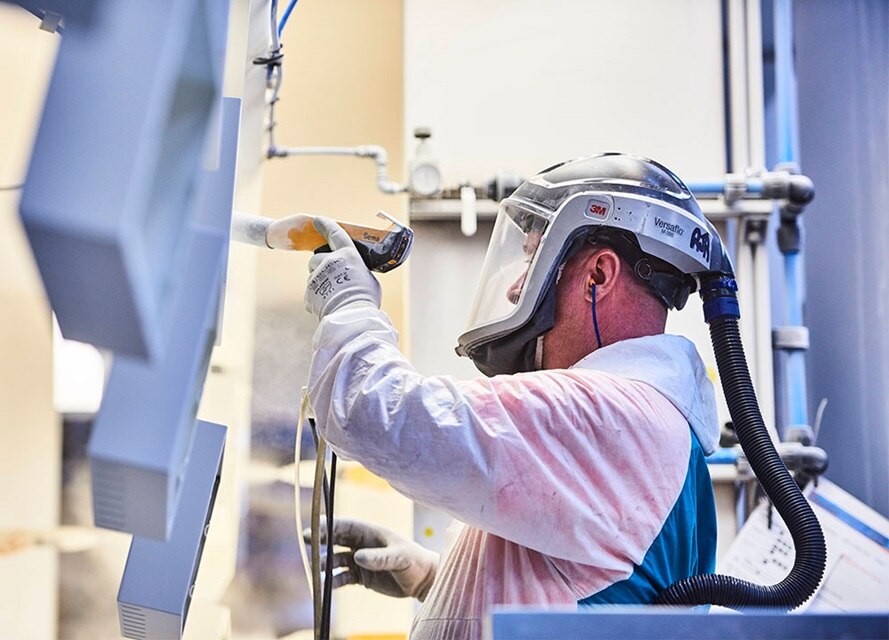
Sustainable Manufacturing | Hager
With the onsite factory responsible for the largest consumption of energy at Hager, the Telford-based manufacturer has carried out significant research to identify where improvements can be made to reduce their environmental impact. Focusing efforts heavily on factory operations, two major energy-consuming processes have been identified that will see a considerable reduction in the factory’s energy usage through the implementation of alternative, more sustainable solutions.
One such process that has been identified, is the chemical bath treatment the steel metal is exposed to prior to powder coating. Once bent into position, taking the form of the consumer unit, the steel components are subjected to a chemical treatment to remove impurities and be thoroughly cleaned. The process involved heating distilled water to 45 degrees, which, long term, consumed a significant amount of energy with the facility in operation 24 hours a day, seven days a week.
To reduce the energy usage required during the process, production managers have dedicated significant attention to researching and developing more environmentally friendly alternatives. As a result of these efforts, improvements have been made to the chemical treatment process to lessen the dependence on energy. Decreasing the temperature of the treatment process from 45 degrees to 25 degrees has resulted in a substantial reduction in energy consumption.
Another area where Hager has focused its sustainability efforts is the powder coating process used to lacquer the enclosures of the consumer units. Manufactured onsite at the Telford-based factory, once painted, the process sees the consumer units placed in an oven where the powder is cured. Extensive testing has been conducted at the lab in Telford to find an alternative powder-coating solution that cures at a lower temperature. Now curing at 180 degrees, down from the previous temperature of 220 degrees, the new powder coating and decrease in temperature used in the curing process have again resulted in a significant reduction in energy consumption.
Taking great care to ensure that the introduction of the new powder coating does not compromise on the quality of the finished product, the extensive testing proved the new powder is just as effective as the old powder coating. Adhering to the enclosures without compromising on the high-quality standards that Hager is known for, installers can be confident that the new finish will provide the same level of durability and aesthetic standard as the previous coating, whilst being manufactured in an environmentally-conscious manner.