Tailored
Solutions
We can provide the right solution that meets your specification.
If your enquiry falls out of the standard offer, Tailored Solutions can meet your requirements.
To discuss your project needs with our technical experts, call us on 01952 675 689, or use the link below to fill out our online form.
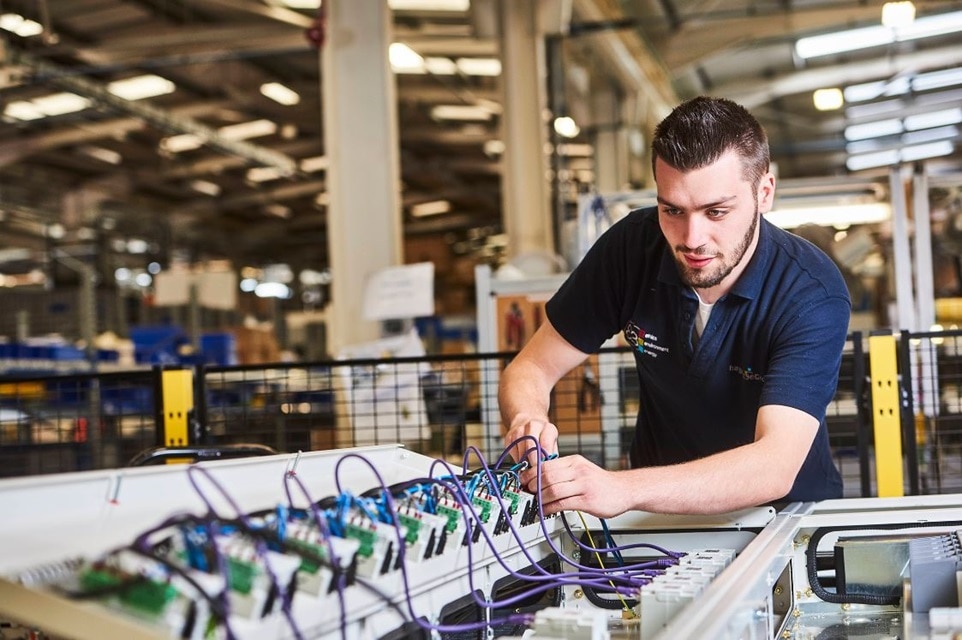
What are Tailored Solutions?
From fitting devices through to bespoke engineering, Tailored Solutions provides a complete service for any project.
For your project, we can offer a solution that can meet the most demanding of challenges. From design & engineering through to logistics, our
Tailored Solutions service offers unrivaled support & peace of mind for you and your business.
Arc Fault Detection
Extra protection. Extra peace of mind.
The 18th Edition of BS 7671 recommends the use of AFDDs to provide additional protection against fire.
Our Tailored Solutions team can help you implement AFDDs in residential or commercial projects.
Popular Examples
We offer a variety of services to suit your project needs
Services
We have a variety of services we offer to accompany our tailored solutions.
Power and lighting board
The requirement for metering in distribution boards is becoming increasingly common with the lighting and power loads needing to be separately monitored. In addition to our standard range of power and lighting boards we have created a number of bespoke solutions.
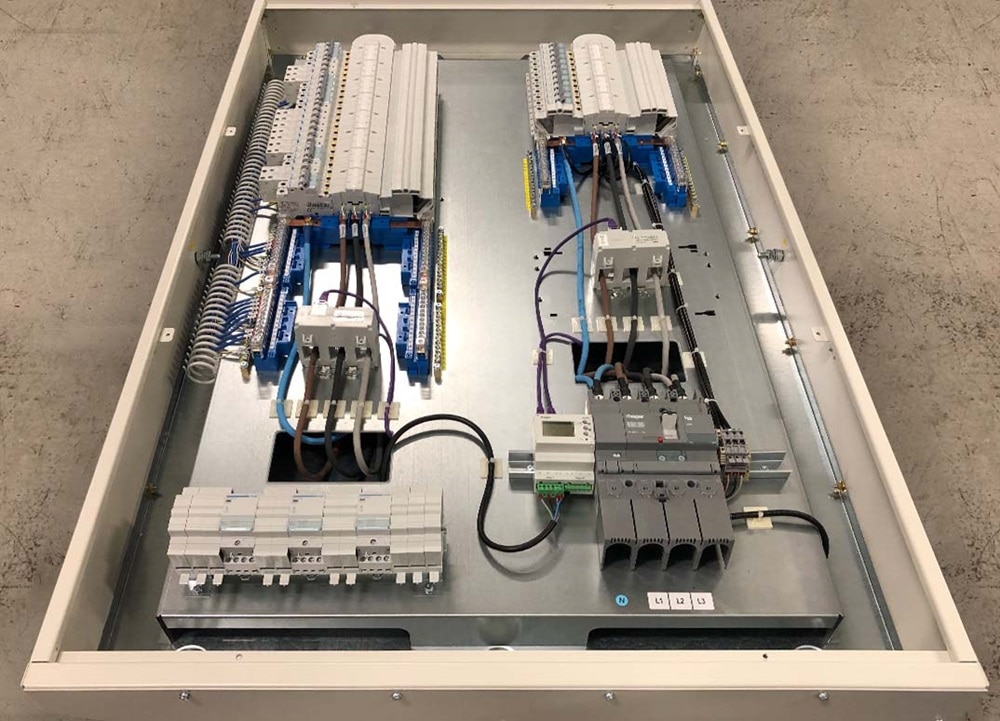
Bespoke Steelwork
Due to our UK-based manufacturing and design capabilities we are able to provide alterations to steel work to suit the requirements of your project.
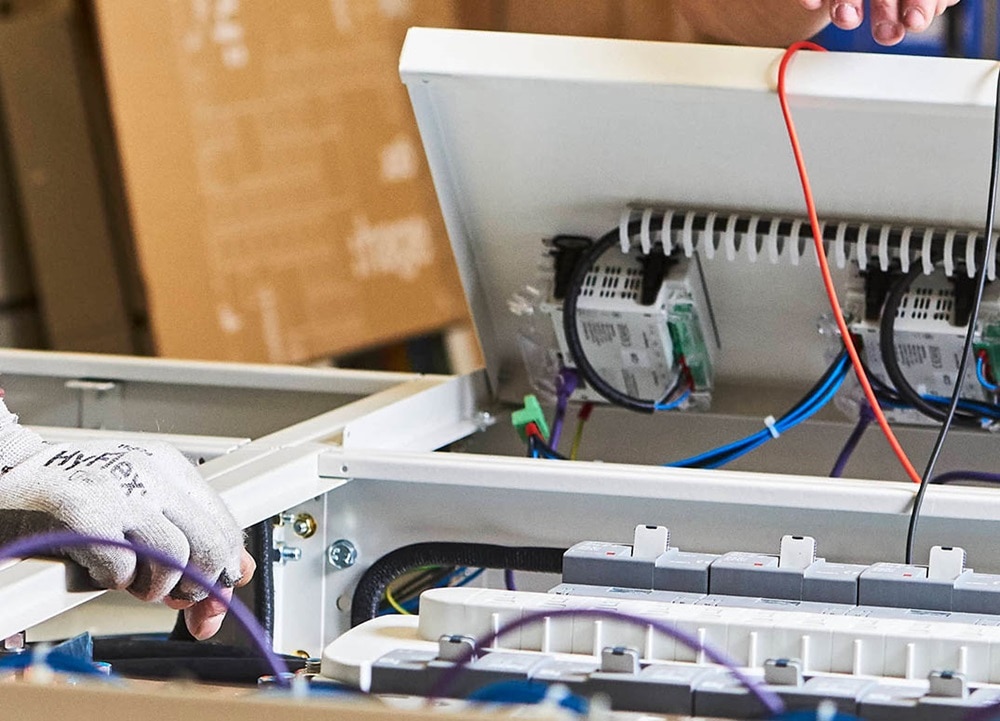
Pre-assembled Enclosures
Your distribution board can be supplied with all outgoing devices, blanks, meters, surge protection etc. factory fitted.
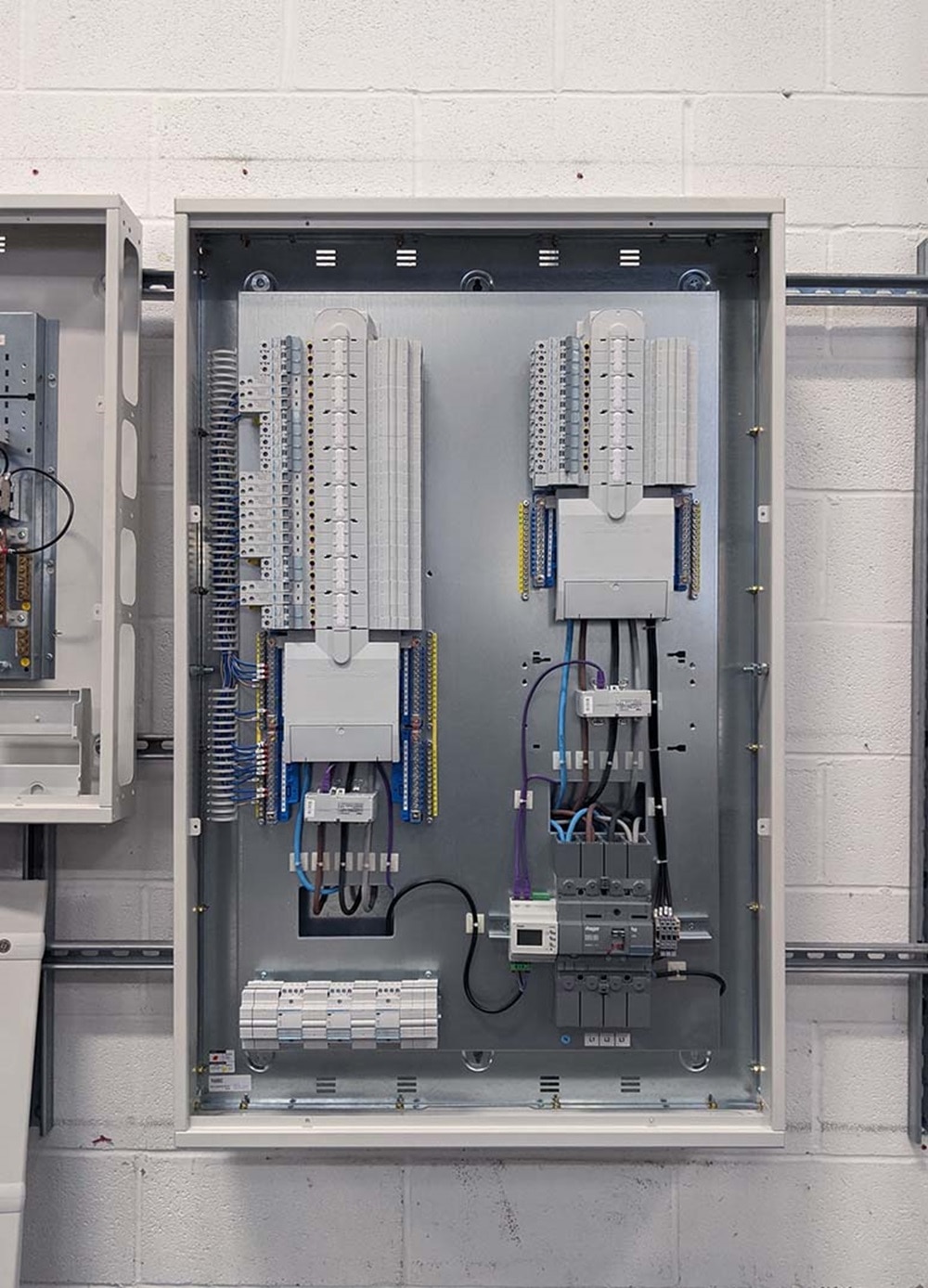
Fuse Combination Switches
Fuse Combination Switches give an option to provide a permanent supply to essential circuits even when the main board is isolated. Connected to the incoming side of the main switch the FCS allows the dedicated circuit to be controlled independently of the main board.
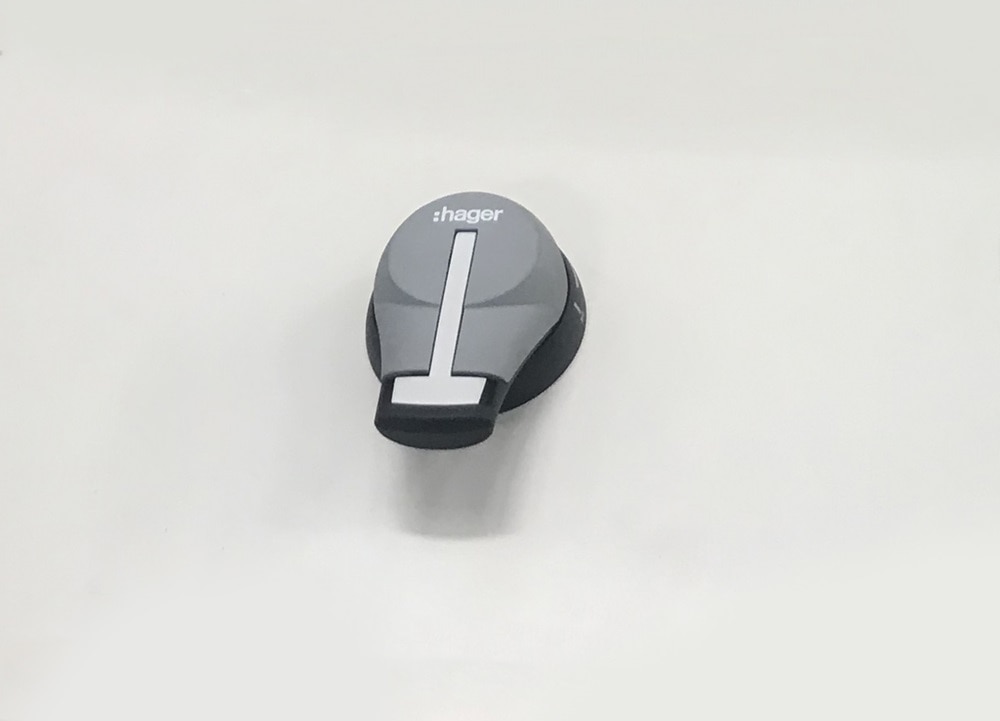
Testing & Validation
Tested, verified and compliant.
Every tailored solution from us comes as a tested assembly to the relevant part of BS EN 61439. With each tailored solution, we take responsibility for the design, verification and the EU declaration of conformity
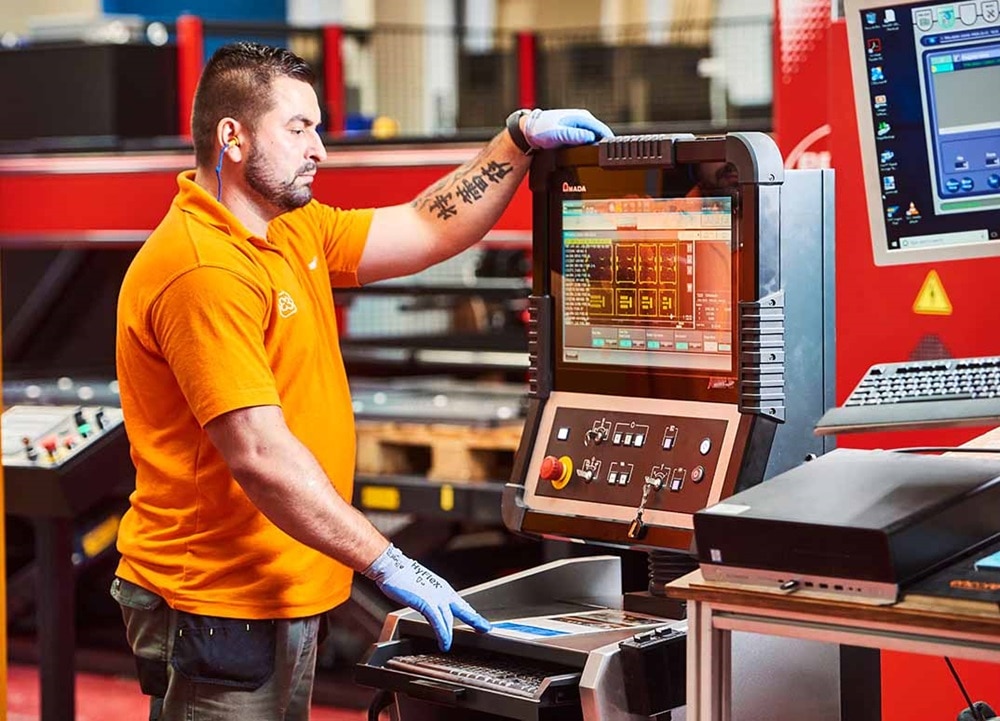
Shipping
Tested and can ship directly to your site
We can ship your tailored solution directly to you, removing the extra loading and unloading through the wholesaler. Our solutions are fully built and tested before being shipped, taking into account the shipping requirements, as well as how the board will be transported to site. Large linked enclosures can be split onto separate pallets to make transportation onsite easier.
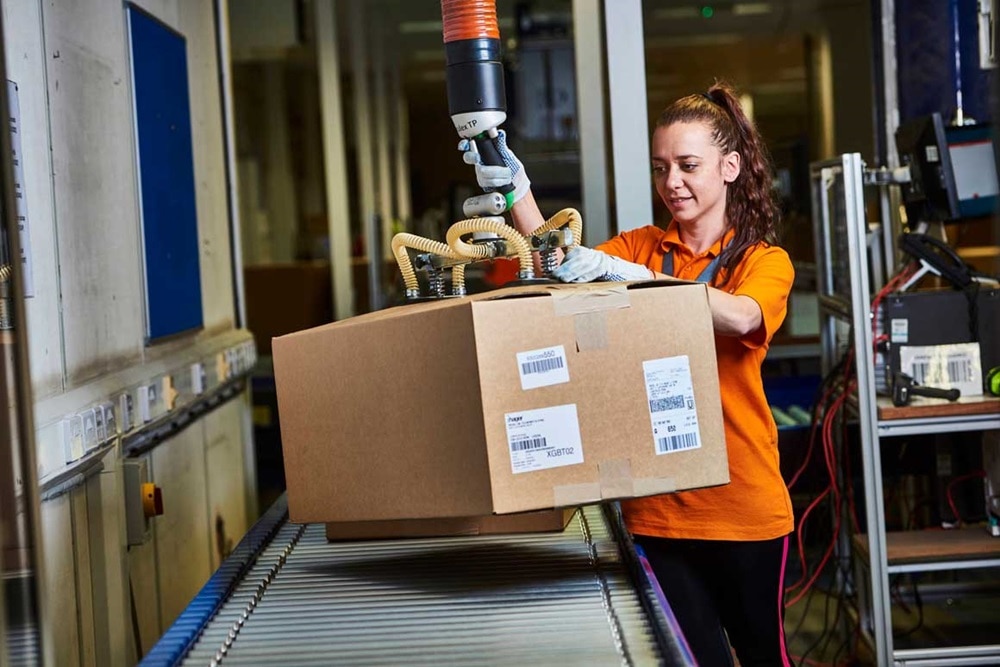
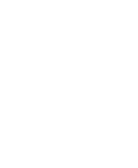
Have a question?
To discuss your project needs with our technical experts, call us on 01952 675 689, or use the link below to fill out our online form.
Have some questions?
Check out our FAQ section to answer some questions you may have.
-
How does the pre-order stage, design and engineering part of the Tailored Solutions service work?
At Hager, our Tailored Solutions service emphasizes precision and customization. In the pre-order stage, we discuss and understand your project needs in depth. Our designers then craft a solution tailored to those requirements. After finalising the design, our engineering team brings it to life, ensuring efficiency, durability, and safety. Throughout, Hager collaborates closely with you to deliver solutions that align with your project's unique demands. -
Can you explain the role of the Tailored Solutions team in providing technical support throughout the project life-cycle?
Hager's Tailored Solutions team is dedicated to ensuring that your project receives the utmost support from conception to completion. From the initial stages, they dive deep into understanding your specific requirements, offering guidance on the best products and configurations for your needs. As the project progresses, they provide timely technical advice to address any challenges or changes that arise, ensuring that solutions are both efficient and compliant. The team's involvement doesn't just end once the product is delivered; they are committed to assisting with installation and post-installation queries. With Hager's Tailored Solutions team by your side, you can be confident of a smooth and well-supported project journey. -
How does the rigorous factory testing process ensure compliance with regulations and specifications for tailored solutions?
At Hager, ensuring our Tailored Solutions meet regulations and specifications is of paramount importance. Our rigorous factory testing process begins by meticulously evaluating each custom solution against set benchmarks. This ensures that every component adheres to industry standards and our own stringent quality checks. Through methodical testing, we ensure not only functionality but also safety, durability, and reliability. Any deviations are promptly addressed, and the product undergoes re-testing until it achieves full compliance. Additionally, us at Hager continuously update our testing methodologies in line with evolving regulations and technological advancements. When you choose a Hager Tailored Solution, you're getting a product that has been put through its paces, ensuring it's up to both your standards and ours.
-
How can the tailored solutions team create bespoke products to suit specific needs of a project?
At Hager, the Tailored Solutions team thrives on adapting to unique project requirements. When faced with a specific need, we begin by closely collaborating with the client to fully understand their specifications and desired outcomes. Drawing on our extensive expertise, we design a prototype that encapsulates these needs. Utilizing state-of-the-art tools and drawing from our vast product portfolio, we ensure that the bespoke product aligns seamlessly with the project's objectives. After a design is settled upon, our dedicated engineering team refines and optimizes it, ensuring it's efficient, compliant, and of the highest quality. The beauty of working with Hager is our agility and commitment. We don't just provide off-the-shelf solutions; we craft unique products that truly resonate with a project's vision and requirements. -
How does the Tailored Solutions team ensure timely and accurate delivery, especially for projects with challenging site conditions and restrictions?
At Hager, our Tailored Solutions team understands the intricacies of diverse projects, especially those with challenging site conditions and restrictions. To ensure timely and accurate delivery:
- Thorough Assessment: Before embarking on any project, we conduct a comprehensive analysis of the site's requirements and challenges. This allows us to anticipate potential obstacles and plan for them.
- Collaborative Approach: We work closely with all stakeholders, ensuring everyone is aligned with the project's goals and timelines. This collaboration ensures that any unforeseen challenges are promptly addressed.
- Dedicated Project Managers: Every tailored project is assigned a dedicated manager who monitors the delivery process, ensuring that all components arrive on site as per the schedule.
- Flexible Logistics: Our logistics team is adaptable, allowing us to adjust to any last-minute changes or requirements that may arise due to site conditions.
- Regular Communication: We maintain open channels of communication with our clients throughout the project. This ensures that you're always updated on progress and any necessary adjustments.
By adopting this proactive and integrated approach, Hager ensures that even the most challenging projects receive their tailored solutions promptly and accurately.